Ecospray is a continuous work in progress: a checkpoint with Giorgio Copelli, Director of Ecospray's Industry & Renewables B.U.
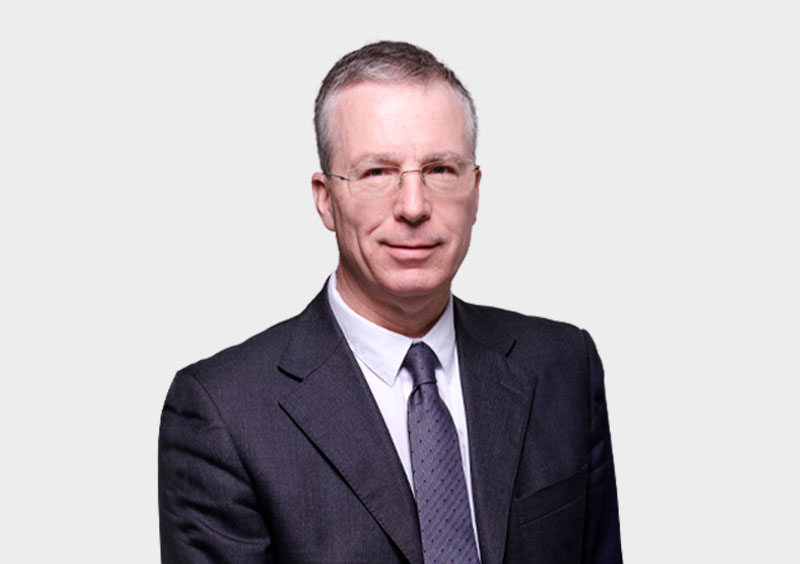
“In addition to the requests we receive for methane and biomethane liquefaction, we get many of them for CO₂ liquefaction, mainly coming from North Europe, where several new plants are about to become operational towards the end of the year, to Central and South America, thanks to the support of a local partner as well“.
A picture that traces an evolution in the entire scope of dedicated decarbonization technologies engineered and implemented by Ecospray.
“I’m thinking of modules to produce food grade CO₂ that will be operational in 2023.” It is, in the latter case, a highly coveted product because it allows a waste product to be turned into a resource, even an economic one.
Copelli explained: “CO₂ in the food industry is currently produced in two main ways: extraction from fossil deposits and combustion of gas. We are facing a huge paradox: CO₂ is being produced in a world fighting for decarbonization. In the second semester of 2023, Ecospray will provide a solution to this impasse, through a constantly modulable plant that produces bio CO₂ – food grade, no less- by capturing it during the production of gas from biomass. This means adding to the benefits of biogas use those from CO₂ sale”.
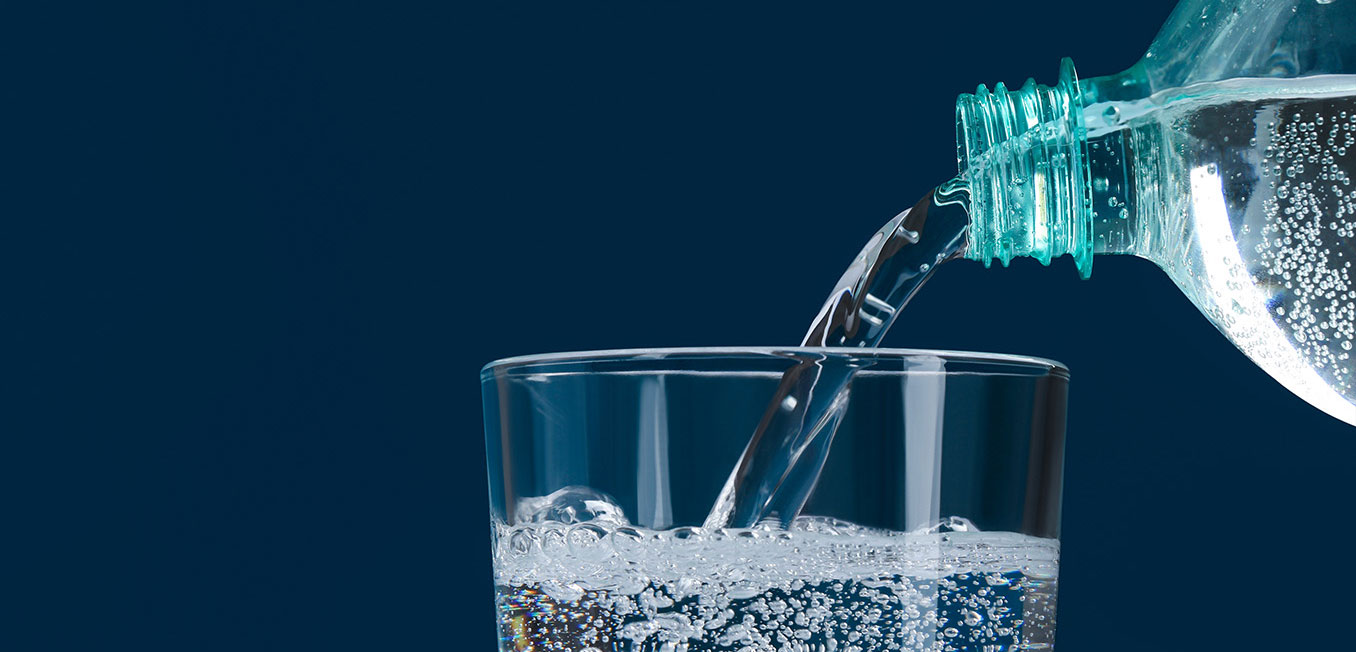
Another agreement with Ruhe Group is being finalized for the supply of several new biomethane micro-liquefaction plants from biomass of livestock origin.
As a particularly appreciated benefice, Ecospray is getting an increasing number of orders in the German market: indeed, another agreement with Ruhe Group is being finalized for the supply of several new biomethane micro-liquefaction plants from biomass of livestock origin.
This growth, both North Europe and in the national and international market, is also explained by the extreme adaptability of the proposed solutions: “Our plants for CO₂ separation, purification and liquefaction are transportable in normal containers and do not involve on-site construction. Installation is quick and without the need for additional masonry work”.
If at the moment the focus is CO₂ liquefaction, as for the near future Copelli has no doubts: one of the greatest bets is the technology developed for OneLNG in order to counter flaring. It is already being tested and will be implemented in a demo plant in a few months. Then, it can be used in all those extraction wells situated in remote locations from where it’s impossible to transport the methane produced during the crude oil extraction process.