Natural Gas Liquefaction
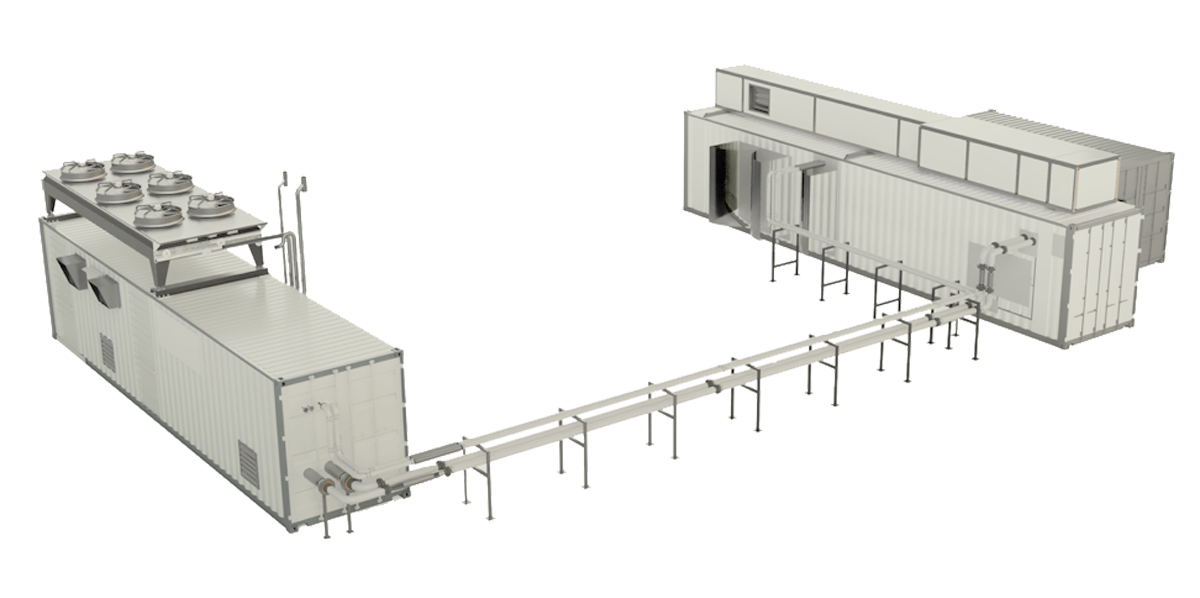
Our micro-liquefaction systems enable on-site LNG production directly from the pipeline. In addition, Ecospray systems can convert a waste product, such as flare gas or APG (associated petroleum gas), into a resource, as NGL and LNG.
Our liquefaction systems are characterized by:
- Faster installation and commissioning due to pre-assembly (fully mounted on skid) and testing in the Ecospray workshop.
- Standard module sizes: 0.5 MMSCFD (10tpd)
- Low energy consumption (< 1 kWh/kgLNG) and high reliability components
- Wide range of LNG outlet temperatures/pressures (subcooling available), std: -149°C @ 4 barg ÷-160°C @ 0,2barg
- Fully automated and remotely controlled for maintenance and monitoring
- Plant modularity allows for incremental LNG production, partial redundancy and significantly reduces local construction.
- No sensitivity to HHC or other components/pollutants ensures NGL-LNG production with any feed gas composition.
- Heavy Hydrocarbon (HHC) separation module available
- Dedicated upstream modules for contaminant treatment (i.e. Hg, H2S, etc.)
- Easily relocatable configuration, useful for shale oil APG, coal methane beds, temporary early production sites
- Stand-alone solutions requiring only electricity and no other utilities (refrigerants, water, compressed air, heat, etc.)
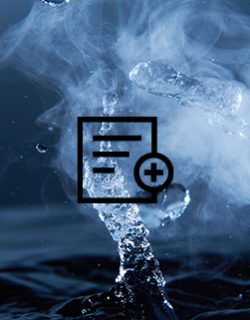