Ecospray introduces One, the new cloud digital solution, recently designed and developed to provide a new range of services to customers.
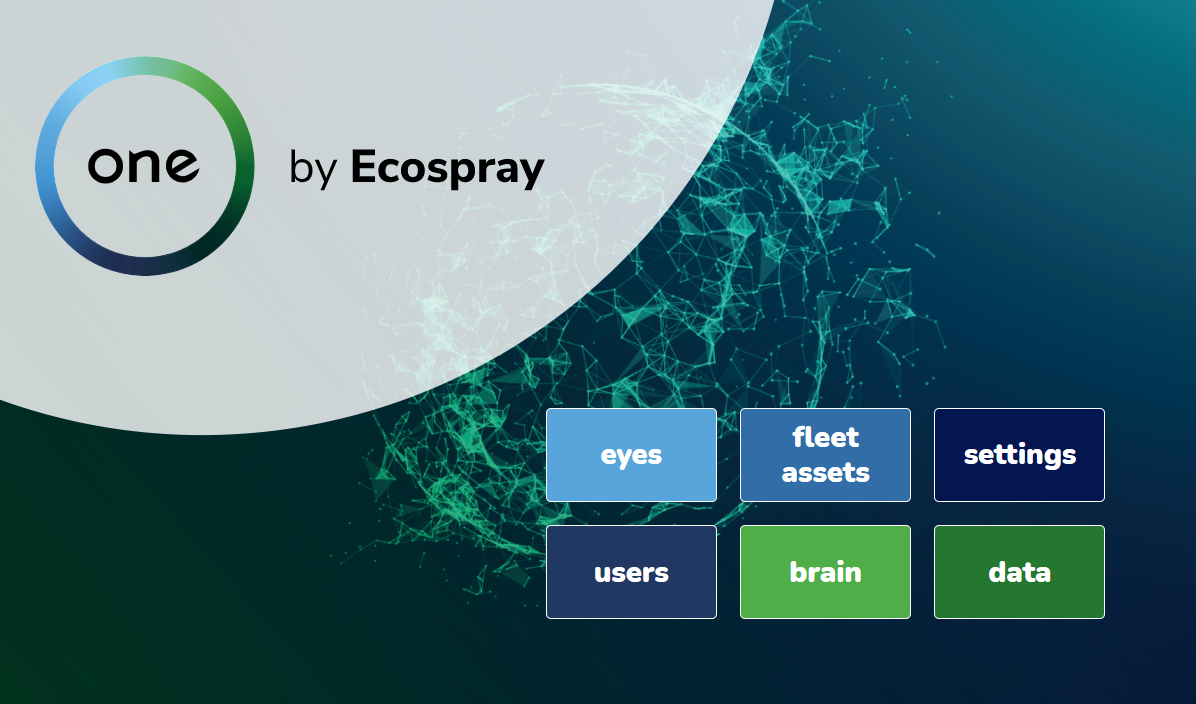
The Challenge
At the heart of the One project, embodied in a powerful easy-to-use digital solution, are the professional figures and technical skills involved in all aspects of the maintenance and operation of a system, process, or structure.
Consistent with Ecospray’s Service & Training approach, providing customer training and support 24/7, the One platform makes it even easier for the customer to manage the system. With One, in fact, support to plant, naval and / or industrial operators is provided in real-time: any problem is identified in the bud and performance data is collected and analyzed digitally.
Through the continuous exchange of information, compliance is guaranteed, asset productivity is increased, and predictive maintenance functions are also available: the passage of maintenance from time indicator or hours/machine, thanks to the precise knowledge of the actual state of wear of the asset can become predictive, also allowing maintenance to be planned with greater precision.
A simple method for solving complex problems
The validity and quality of data are no longer a real challenge, technologies are now widely available. The critical issue is the actual usefulness of the data: it is in fact necessary to have the technical skills to better interpret the data and generate information flows that allow the Customer to intervene quickly and strategically.
Until now, Big Data coming from the integration of field instrumentation – DCS and control systems, are often available in formats that are not meaningful to the management and shared with the competent technician late in respect to the need arising.
With One, companies can move from simple data collection to their structuring, processing and analysis, allowing specialists with different skills to work together: both on a technical and a strategic level.
Our digital solution is designed to share data with the work group, even if heterogeneous: this approach is key to obtaining greater reliability, productivity, and operational excellence of the system, transforming passive data into useful information to allow different stakeholders to take informed decisions.
But that’s not all: the ability to analyze data is significant to the point of being able to guide operational decisions, increasing the productivity and profitability of the system to a minimum, unscheduled downtime.
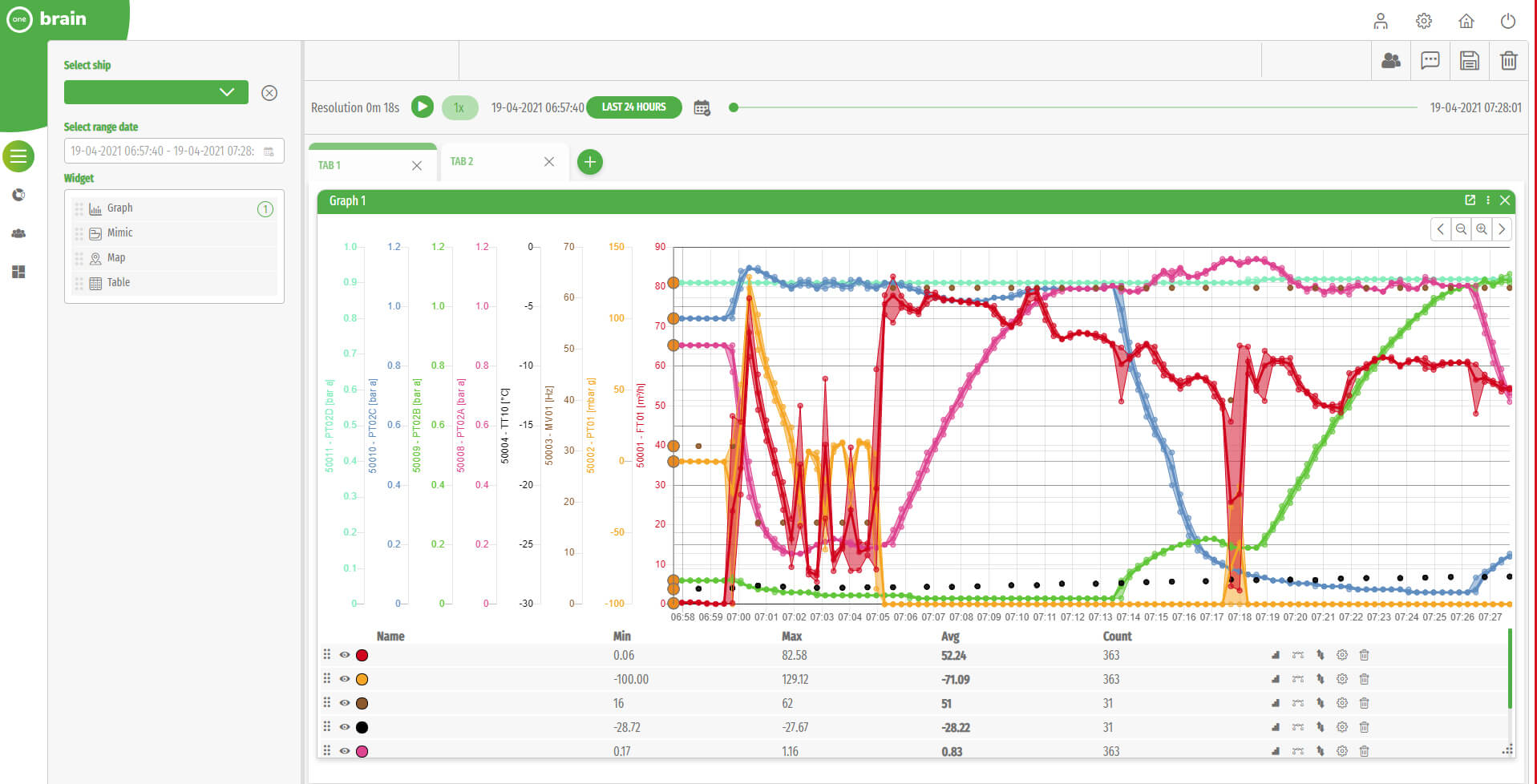
How does it work?
Data is acquired from the automation systems using a modern digital communication infrastructure. The information is transmitted encrypted and made available via authentication to Ecospray technicians, operators, and plant managers, anywhere and at any time.
Using the processing capacity available on the cloud and on “edge-computing”, the data coming from the system is processed through analyzers that return information on the state of the system: conditions, remote diagnostics, performance monitoring, IT security and predictive maintenance.
In conclusion
One is of fundamental utility to allow customers to focus their resources on results such as improving productivity, reducing downtime and equipment breakdowns, reducing asset maintenance costs but also optimizing overall business performance.
All this is possible only thanks to the emphasis we wanted to place on security: a guarantee that protects data, people, and resources at every level of integration. In addition, a team of experts is available at the Ecospray Operation Centre, 24/7.